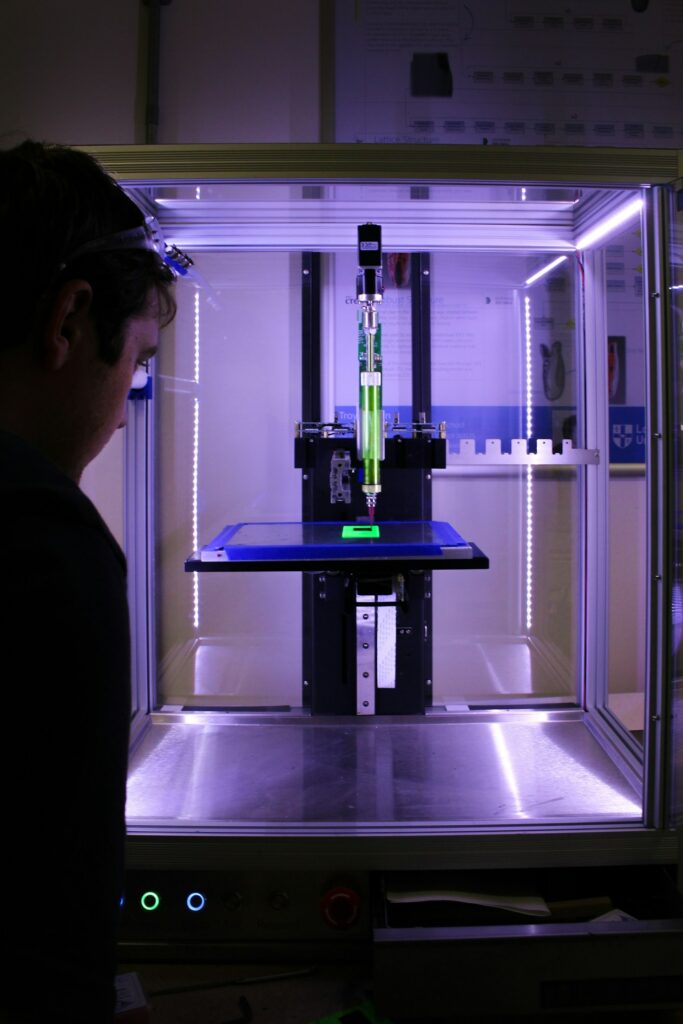
Additive manufacturing (AM), commonly known as 3D printing, is transforming industries by enabling faster, more flexible production. Unlike traditional manufacturing, which removes material to shape a final product, AM builds objects layer by layer using digital designs.
This approach allows for intricate designs, reduces waste, and shortens production timelines. As a result, industries like aerospace, healthcare, and automotive are rapidly adopting AM technologies to improve efficiency and innovation.
This guide explains the core principles of additive manufacturing, the different types of AM processes, and how the technology is shaping industries and careers.
Table of Contents:
How Additive Manufacturing Works
Additive manufacturing starts with a computer-aided design (CAD) file, which serves as the blueprint for printing. The digital model is then sliced into thin layers, and a 3D printer builds the object one layer at a time.
The process varies depending on the type of AM technology used. Some systems melt or fuse materials with lasers, while others use liquid resins or powders that harden layer by layer.
AM is particularly useful for rapid prototyping and low-volume production, allowing manufacturers to create complex parts that would be difficult or impossible to produce with traditional methods.
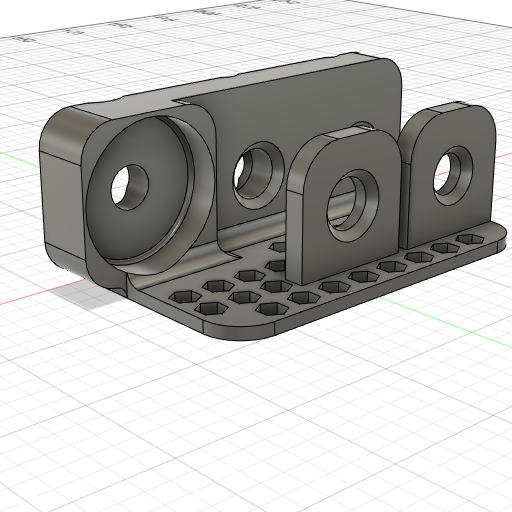
Types of Additive Manufacturing Technologies
There are several types of additive manufacturing, each suited for different applications and materials. The most common methods can be viewed below:
Technology | Process | Materials Used | Advantages | Common Applications |
---|---|---|---|---|
Fused Deposition Modeling (FDM) | A thermoplastic filament is melted and extruded through a heated nozzle, layer by layer. | PLA, ABS, PETG, Nylon, TPU | Low cost, easy to use, widely available | Prototyping, consumer goods, educational models |
Stereolithography (SLA) & Digital Light Processing (DLP) | A laser (SLA) or light projector (DLP) cures liquid resin layer by layer. | Photopolymer resins | High resolution, smooth surface finish | Dental models, jewelry, medical prototypes |
Selective Laser Sintering (SLS) | A laser fuses powdered polymer particles into solid layers. | Nylon, TPU, composites | Strong parts, no need for support structures | Aerospace, automotive, functional prototypes |
Direct Metal Laser Sintering (DMLS) & Selective Laser Melting (SLM) | A laser sinters (DMLS) or fully melts (SLM) metal powder layer by layer. | Titanium, stainless steel, aluminum, cobalt-chrome | High strength, complex geometries, industrial-grade durability | Medical implants, aircraft components, custom tooling |
Binder Jetting | A liquid binder selectively fuses powdered material. Parts are later sintered or infiltrated with another material. | Sand, metal, ceramic, gypsum powders | Cost-effective, full-color printing available | Sand casting molds, full-color prototypes, metal parts |
Material Jetting | Print heads deposit liquid photopolymers or wax layer by layer, which harden via UV light. | Photopolymer resins, wax | Extremely high precision, multi-material printing possible | High-detail prototypes, dental models, visual prototypes |
Multi Jet Fusion (MJF) | A fine detailing agent is applied to powdered material and fused by a heat source. | Nylon, TPU, PA12, composites | High speed, strong and detailed parts | Functional prototypes, industrial parts, healthcare |
Concrete 3D Printing | A robotic arm extrudes a cement-based material layer by layer to create large structures. | Concrete, geopolymer, sand mixtures | Fast construction, reduced material waste | Housing, infrastructure, bridges |
Applications of Additive Manufacturing
Aerospace
The aerospace industry uses AM to create lightweight, high-strength components. Airbus has integrated 3D-printed parts into its aircraft, reducing weight and improving fuel efficiency (Airbus).
Automotive
Car manufacturers use AM for both rapid prototyping and end-use parts. Companies like Bugatti 3D print performance parts, such as suspension parts, to reduce weight and enhance customization (3Dprint.com).
Medical & Dental
The healthcare sector relies on AM for patient-specific prosthetics, implants, and surgical guides. In dentistry, 3D printing is used for crowns, bridges, and aligners, improving patient care with custom-fit solutions.
Construction
AM is revolutionizing the construction industry by enabling 3D-printed houses, bridges, and infrastructure. In some cases, entire 3D-printed buildings are being constructed, reducing costs and material waste.
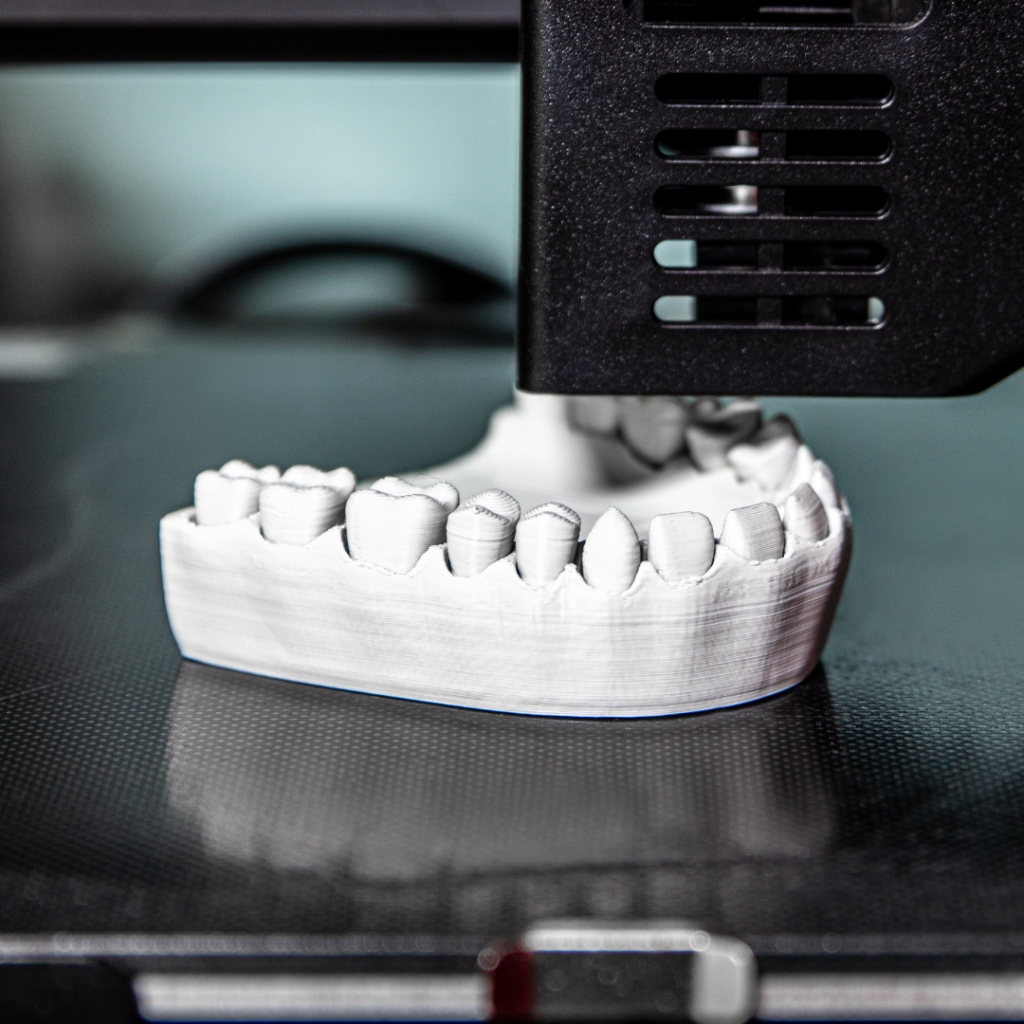
Advantages and Challenges of Additive Manufacturing
Advantages
Benefit | Description |
---|---|
Design Flexibility | AM allows for complex geometries and lightweight structures. |
Reduced Waste | Material is added only where needed, minimizing waste. |
Customization | Products can be tailored to individual needs, such as medical implants. |
Faster Production | Prototyping and manufacturing times are significantly reduced. |
Challenges
Challenge | Description |
---|---|
High Initial Costs | Industrial 3D printers and materials can be expensive. |
Material Limitations | Not all materials are suitable for AM processes. |
Post-Processing Needs | Many parts require sanding, polishing, or sintering after printing. |
Future of Additive Manufacturing
The global additive manufacturing (AM) market is on a trajectory of explosive growth. Valued at $20.37 billion in 2023, it is expected to expand at a compound annual growth rate (CAGR) of 23.3% from 2023 to 2030 (Grand View Research). By the end of the decade, AM could redefine how industries approach production, supply chains, and material science, setting the stage for a new industrial revolution.
Traditionally, 3D printing was seen as a prototyping tool, allowing engineers to create and test designs before committing to large-scale manufacturing. However, advances in speed, material diversity, and AI-driven automation are making it possible to mass-produce end-use parts.
The future of manufacturing is autonomous and data-driven. AI-powered additive manufacturing systems will:
- Self-optimize print parameters in real time for perfect precision.
- Detect and correct errors mid-print, reducing waste and improving efficiency.
- Integrate seamlessly with robotics, enabling fully automated production lines.
Sustainability is also becoming a top priority in global manufacturing, and AM is poised to lead the way. Unlike traditional subtractive manufacturing, which wastes up to 60% of raw materials, additive processes use only the necessary amount of material.
Perhaps the most futuristic application of AM lies in bioprinting. By 2035, scientists could achieve functional 3D-printed organs, reducing dependency on human donors and organ transplant waiting lists.
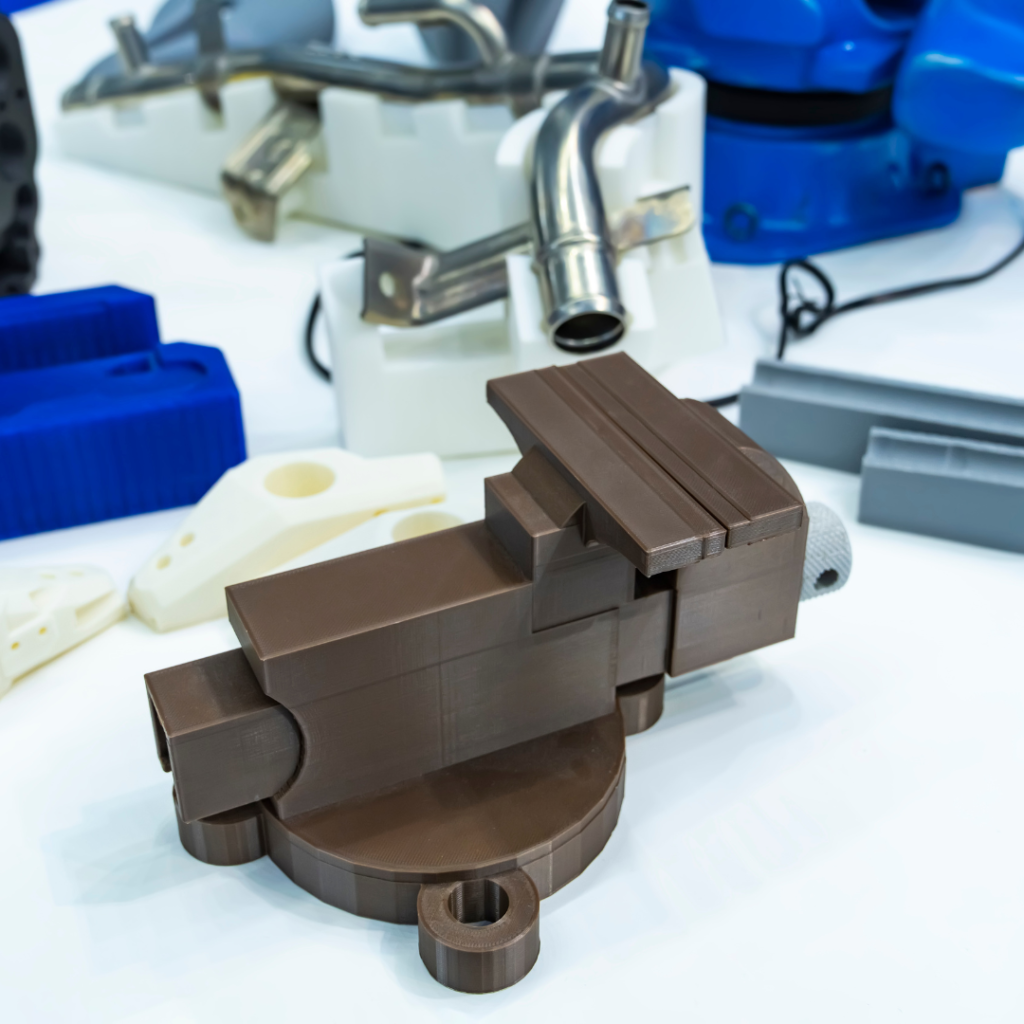
Conclusion
Additive manufacturing is revolutionizing industries by enabling faster, more efficient production with minimal waste. From aerospace to healthcare, companies are leveraging AM to produce complex, high-performance components that were once impossible to manufacture.
As AM technology advances, new career opportunities will emerge, and industries will continue to innovate with 3D printing. Whether you’re exploring a career in AM or looking to adopt the technology in your industry, understanding the fundamentals is the first step toward embracing this cutting-edge manufacturing revolution.
Leave a Reply